Microchips, the tiny powerhouses behind modern electronics, come to life through a detailed and intriguing process. But how exactly are these microchips created? This article takes a deep dive into the intricate journey from simple silicon to complex electronic parts.
To fully grasp this process, it’s also helpful to look at the evolution of the microchip, following its development and progress over time.
These small parts, which run everything from everyday gadgets to high-tech computer systems, are made through a highly advanced production process. This process, while complicated, can be generally divided into three main steps: making the blank wafer, building the chip (fabrication), and protecting the chip (encapsulation). Each step is a testament to the wonders of engineering and science, showcasing the continuous drive for technological progress.

This article not only uncovers the process of making microchips, but also sheds light on the creation of a computer chip, from the basic materials to the finished product. The inquiry into how microchips are produced takes us on an exciting journey into the realm of microchip production.
The Three Fundamental Phases in the Production of a Microchip
Before we get into the details of how microchips are made, it’s important to know that there are three main steps involved. Each step is key in turning a simple piece of silicon into a complex and working microchip.
Making the Blank Wafer: The journey of a microchip starts with the creation of blank wafers. These wafers are usually made from silicon because it’s a great semiconductor. The process starts with growing silicon crystals, which are then cut into thin, shiny discs. This first step is very important because it prepares the base for the detailed layers and structures that will be added later.
Fabrication: After the blank wafers are made, the next step is fabrication. This is where the real transformation happens. Through a series of carefully controlled processes, including photolithography, doping, etching, and deposition, detailed circuits are etched onto the wafer. Every step in this phase needs to be done with utmost precision and control, as even the smallest mistake can make the chip useless. The fabrication process is not just a showcase of human accuracy but also a reflection of the progress in nanotechnology and material science.
Encapsulation: The last step in the making of a microchip is encapsulation. Once the wafer is filled with countless tiny circuits, it needs to be protected. Encapsulation involves covering the delicate structures in a protective material, keeping them safe from physical harm and environmental factors. This step is crucial for making sure the microchip lasts long and works reliably, especially considering the harsh conditions they often have to work under.
Now that we’ve outlined the main framework of microchip manufacturing, let’s dive into the first important phase of this complex process: Growing the Wafer.
Wafer Cultivation: A Crucial Phase in the Production of Microchips
In simpler terms, the process of growing wafers is a key part in making microchips. It’s a careful and precise process that allows us to put thousands of tiny devices onto a single wafer. This makes the manufacturing process more efficient and helps to lower the cost.
Now, let’s take a closer look at how wafers are grown. It’s a process that requires both scientific knowledge and a touch of artistry in the field of semiconductor production.
The creation of silicon chips starts with this important step of growing wafers. This is usually done using a specific method known as the Czochralski method.
The Czochralski method: The Craftsmanship Involved in Shaping Silicon Wafers
To put it in simpler terms, the creation of a silicon chip involves a key technique known as the Czochralski method.
- Starting the Process: The process of making wafers starts with the Czochralski Method. This method has been used for over a hundred years to produce silicon wafers. It starts with a small, carefully selected seed crystal made of pure silicon.
- The Important Dip and Lift: The seed crystal is gently dipped into a melted pool of silicon. As it’s slowly lifted out, it’s also rotated. This combination of slow lifting and rotation is vital for the growth process.
- Adding Impurities for Different Types of Semiconductors: To adjust the semiconductor properties of the silicon, certain impurities, known as dopants, are added to the melted silicon. Elements like Boron and Phosphorus are often used to create either p-type or n-type semiconductors. Each type has unique electrical properties that are crucial for different functions of a microchip.
- Growing a Uniform Crystal: As the seed crystal is pulled out from the melted pool, a large, uniform cylinder of silicon, called an ingot, forms underneath it. The Czochralski Method ensures that this ingot is a single crystal without any flaws. This uniformity is important not just for the structure but also for the functionality of the semiconductor. The performance of a microchip depends on the purity and perfection of the crystal.
- From Ingot to Wafer: Once the single-crystal silicon ingot is fully grown, it’s cooled down. The next step is to cut this ingot into thin, large wafers using high-precision diamond blades. The size of these wafers can vary, usually between 100mm to 300mm, depending on the needs of the microchip being made.
The careful process of growing and preparing silicon wafers is just the beginning. The next important phase in microchip production is wafer fabrication. This is where the carefully prepared wafers are transformed into microchips.
Picturing the Czochralski Technique: Animation of Silicon Ingot Formation
The article gives a thorough explanation of the Czochralski Method. To make it easier to understand, there’s a video that shows a colorful animation of how a silicon ingot grows inside a special type of furnace known as an LCT. This animation is provided by a company called Linton Crystal Technologies. It helps us see the complex process of growing silicon crystals, which is a very important part of making microchips. By watching the animation, you can see the theory behind the Czochralski Method in action.
Microchip Production: The Detailed Art of Making Wafers
The process of making microchips goes on with a step called wafer fabrication. In this step, factories that make semiconductors turn clean silicon wafers into complicated electronic devices. This part of the process is a careful mix of chemistry, physics, and very small technology, and it involves several steps to create individual layers on the silicon wafer.
To understand better how a semiconductor chip is created, we’ll take a closer look at the steps in wafer fabrication. This part of the article gives a detailed view of how electronic chips are made, with a focus on the process of fabricating the wafer.
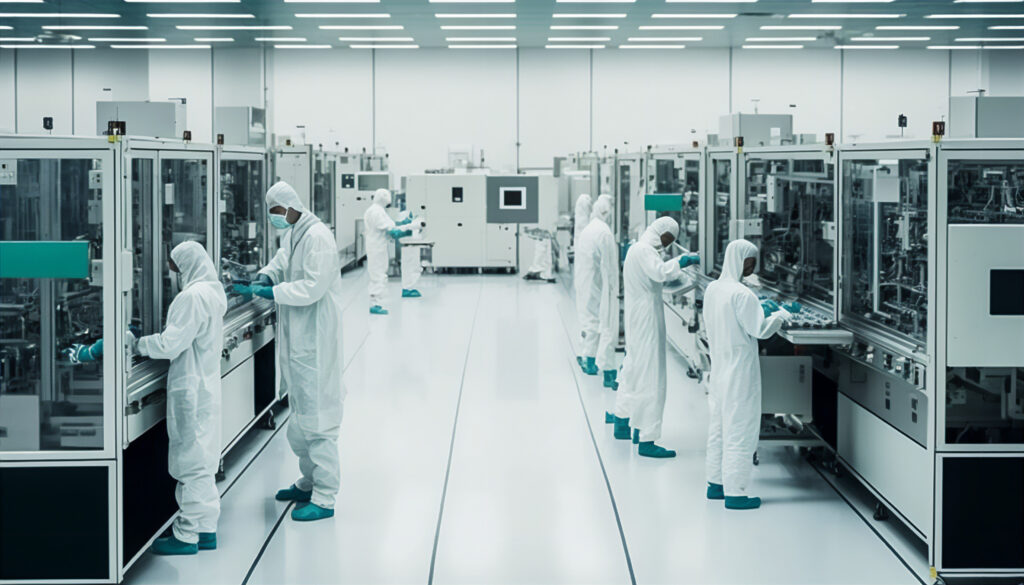
In-Depth Process of Wafer Fabrication
Making semiconductor chips is a complex process that involves many cycles of layering, creating patterns, and etching.
- Getting Ready: The process starts with a thorough cleaning of the wafers to prepare them for the detailed fabrication process. It’s very important to correctly align the wafers at this stage because of their crystal structure, which needs to be precisely aligned for the next steps.
- Growing the Oxide Layer: The first step in layering is to grow an oxide layer on top of the wafer. This layer is very important because it controls the doping process, which changes the electrical properties of the semiconductor.
- Applying Photoresist and UV Imaging: Next, a layer of photoresist, which is sensitive to light, is applied to the wafer. The image of the doped regions is projected onto the photoresist using ultraviolet (UV) light. This step is crucial for creating the detailed patterns of the microchip’s circuits.
- Development and Etching: After being exposed to UV light, the photoresist is developed, and the areas that weren’t exposed are removed. A strong acid, like Hydrofluoric acid, is then used to etch away the oxide areas that aren’t protected by the photoresist.
- Doping Process: At this stage, dopants are added to the semiconductor. The areas not covered by photoresist absorb these dopants, changing their electrical properties to create N and P type regions, which are essential for the function of transistors.
- Adding More Oxide Layer and Forming Gates: Another oxide layer is grown over the entire wafer, which serves as the base for transistor gates. A new layer of photoresist is applied, and the gate structure is imaged onto the wafer using UV light. The following development and etching process creates the semiconductor regions that form the transistors.
- Fabricating Interconnects: The last stage involves making interconnects, which connect the various semiconductor regions. Unlike oxide layers, interconnect layers are made from metals like aluminum, which are deposited using vacuum deposition techniques. These metal layers are then patterned with resist and etched, similar to the earlier steps.
- Layering and Patterning: The process of layering, applying photoresist, developing, and etching is repeated to create the interconnects. A chip can have up to 15 interconnect layers, but designers usually aim for between 3 and 6 layers to balance complexity and functionality.
Wafer fabrication is a testament to the complexity and precision involved in making microchips. In this phase, a simple silicon wafer undergoes an amazing transformation into a microchip. This process isn’t just one step but a series of multiple cycles involving layering, patterning, and etching. Each of these steps is carefully carried out, building up the tiny structures that eventually define the microchip.
The fabrication process is more than just imprinting designs onto silicon. It’s like a symphony of advanced technological processes, each playing a crucial role. From the careful application of photoresist to the precision of the final etching, every action requires not only exact control but also a deep understanding of material properties and semiconductor physics.
Encapsulation: The Last Step in the Production of Microchips