In the previous section, we discussed the definition and the history of Power Electronics. Today, we will continue to explore the main components, dimensions, and heat dissipation issues of power circuits.
Essential Elements of Power Electronics
Power electronics is a field that relies heavily on several crucial components, each of which plays a significant role in the management and transformation of electrical power. Over time, these components have undergone substantial evolution to adapt to the varying requirements of different applications.
Semiconductors (Diodes, Transistors):
The foundation of power electronics lies in semiconductors, with diodes and transistors being the most basic elements.
- Diodes: Diodes, which permit current flow in only one direction, are vital for rectification processes. They have progressed from vacuum tube diodes to semiconductor diodes, encompassing Silicon, Germanium, and more recently, Silicon Carbide (SiC) and Gallium Nitride (GaN) diodes. Each progression has brought about enhancements in efficiency, speed, and thermal performance. For example, SiC diodes are commonly used in high-voltage applications due to their capacity to function at higher temperatures and voltages with superior efficiency.
- Transistors: Transistors, including Bipolar Junction Transistors (BJTs), Field-Effect Transistors (FETs), MOSFETs, and IGBTs, serve as switches or amplifiers in power electronic circuits. The transition from BJTs to MOSFETs and IGBTs signified a notable enhancement in power handling abilities and switching speeds. MOSFETs, for instance, are favored in low to medium power applications due to their high switching speed and efficiency, while IGBTs are preferred in high power applications for their high current and voltage handling capabilities.
Converters (AC to DC, DC to AC, DC to DC, AC to AC):
Converters play a pivotal role in altering the form of electrical power to accommodate different applications.
- AC to DC (Rectifiers): Rectifiers transform alternating current (AC) to direct current (DC). They vary from simple single-phase diode bridges to intricate three-phase controlled rectifiers, utilized in applications such as battery charging and DC motor drives.
- DC to AC (Inverters): Inverters change DC to AC and are vital in applications like solar power systems and electric vehicles. Contemporary inverters not only convert power but also modify frequency and voltage to align with grid requirements or specific load needs.
- DC to DC (DC Converters): These converters adjust the level of DC voltage and are employed in applications like power supplies for electronic devices, where different components necessitate different voltage levels.
- AC to AC (AC Converters): AC converters, including cycloconverters and matrix converters, alter the frequency and voltage of AC power. They are utilized in applications like variable-speed AC motor drives.
Controllers and Regulators:
Controllers and regulators are indispensable for overseeing the performance of power electronic systems.
- Controllers: These components supervise the operation of converters and inverters, ensuring that the output aligns with the desired criteria. They range from simple analog circuits to sophisticated digital controllers using microprocessors or DSPs. Controllers are crucial in applications like motor drives, where precise control of speed and torque is required.
- Regulators: Voltage and current regulators keep the output of power electronic systems at a steady level, despite variations in load or input voltage. They are fundamental in power supplies and battery chargers to safeguard sensitive electronic components from voltage fluctuations.
In conclusion, the components of power electronics – semiconductors, converters, controllers, and regulators – have undergone significant evolution, propelled by advancements in materials science, semiconductor technology, and digital control techniques. Their ongoing development has broadened the capabilities of power electronic systems, enabling more efficient, reliable, and compact solutions for a diverse range of applications.
Considerations on Energy Efficiency and Sizing
Efficiency in power electronics is not merely an attractive quality; it’s a crucial element that profoundly influences energy consumption and system performance. This section delves into the importance of efficiency in power electronic systems and examines the ongoing challenges and solutions in reducing the size of these devices.
Significance of Efficiency:
- Power Usage: The efficiency of power electronic devices has a direct impact on the amount of electrical energy transformed into heat. Greater efficiency implies less energy is wasted as heat, resulting in decreased energy consumption. This is especially important in applications like renewable energy systems and electric vehicles, where optimizing energy use is essential.
- Operational Efficiency: Efficient power conversion guarantees the best performance of the end-use equipment. For example, in an electric vehicle, more efficient power electronics can result in extended battery life and driving range.
- Heat Control: High efficiency helps mitigate thermal management issues. Power electronic devices produce heat during operation, and excessive heat can cause reliability problems and a reduced lifespan. Efficient devices produce less heat, simplifying cooling needs and improving overall reliability.
Challenges in Reducing Size:
The task of reducing the size of power electronic devices while maintaining or enhancing their efficiency is a significant engineering challenge. Smaller devices are preferred for their compactness, which is crucial in space-limited applications like mobile devices and aerospace.
- Heat Management: As devices become smaller, the heat produced per unit area increases, making thermal management more difficult. Efficient heat dissipation methods are essential to prevent overheating in miniaturized devices.
- Limitations of Materials: The physical properties of materials used in semiconductors set boundaries on miniaturization. Innovations in materials like SiC and GaN have been key in overcoming some of these limitations, providing better performance at smaller sizes.
- Complexity in Fabrication: The production of smaller power electronic components often involves more intricate manufacturing processes, which can raise costs and affect scalability.
Examples of Enhancements in Efficiency:
- Solar Power Systems: In solar inverters, advancements in power electronics have led to higher conversion efficiencies, enabling more solar energy to be converted into usable electrical power. Modern inverters achieve efficiencies of over 98%, significantly enhancing the feasibility of solar installations.
- Electric Vehicles: The development of compact, high-efficiency power electronic systems in electric vehicles has been key in increasing their range and performance. For instance, the use of advanced SiC-based power electronics in some electric vehicles has led to efficiency improvements, contributing to longer battery life and extended range.
- End-User Electronic Devices: The reduction in size of power supplies for consumer electronics, like laptops and smartphones, has seen significant advancements. Modern power adapters are not only smaller but also much more efficient, reducing energy waste and improving user convenience.
To sum up, efficiency and compactness are intertwined aspects in the creation and evolution of power electronic systems. Striking an optimal equilibrium between these two elements is crucial to cater to the needs of contemporary applications, ranging from handheld devices to extensive industrial systems. The persistent advancements in materials, design, and manufacturing methodologies persistently broaden the horizons in power electronics, with the goal of developing tinier, more efficient, and more dependable systems.
Thermal Dissipation and Heat Management Techniques
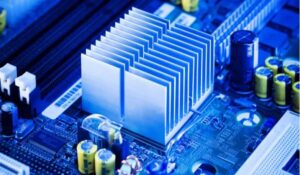
Efficient heat regulation is a vital component of power electronics, particularly as devices evolve to be more potent and smaller in size. This section offers an extensive review of heat management strategies, encompassing recent progress, and showcases examples that illustrate these strategies in applications involving high power.
Strategies for Managing Heat:
- Heat Sinks and Cooling Mechanisms: Conventional heat sinks, constructed from materials with superior thermal conductivity like aluminium or copper, are extensively employed to dissipate heat in power electronic devices. Progress in heat sink design, including optimised fin configurations and liquid cooling systems, have markedly enhanced heat dissipation efficiency.
- Thermal Interface Substances (TIMs): TIMs, such as thermal pastes, pads, and epoxies, are utilised to enhance the thermal contact between the heat source (for instance, a semiconductor device) and the heat sink. Recent advancements in TIMs concentrate on materials with increased thermal conductivity and extended operational lifespan.
- Cutting-Edge Cooling Methods: Methods like phase-change cooling, where a fluid absorbs heat and undergoes a phase transition (from liquid to gas), provide efficient cooling for high-power applications. Microchannel cooling, where minuscule channels are carved into a substrate to facilitate fluid flow, delivers effective heat dissipation in a compact form factor.
- Incorporation of Cooling into Device Design: Contemporary power electronic devices are progressively designed with integrated cooling solutions. For instance, incorporating cooling channels directly into the substrate or the semiconductor package enables more direct and efficient heat extraction.
Examples of Heat Management:
Electric Vehicle Power Electronics: In electric vehicles (EVs), power electronic elements such as inverters and converters deal with high power levels, producing substantial heat. Advanced cooling mechanisms, often involving liquid coolants, are utilized to maintain ideal operating temperatures. For example, certain EV models employ integrated cooling plates that are thermally linked to the power electronic elements, ensuring effective heat dissipation.
- Industrial Motor Drives: Industrial motor drives with high power require sturdy thermal management to handle the heat produced by power semiconductors. Case studies have demonstrated the effectiveness of liquid cooling systems in these applications, where coolant is circulated through heat exchangers directly connected to the power modules. This method allows for higher power density and enhanced reliability.
- Renewable Energy Systems: In solar inverters and wind turbine converters, heat management is vital for performance and durability. Advanced air-cooling and liquid-cooling methods are used to manage the thermal load. For instance, some high-capacity solar inverters use sophisticated air-cooling systems with intelligently designed airflow paths and heat sinks to maintain optimal temperatures.
In conclusion, thermal management in power electronics is a complex challenge that necessitates a blend of materials, design, and advanced cooling technologies. As power densities rise and devices become more compact, the significance of efficient heat dissipation becomes increasingly critical. The continuous innovations in thermal management techniques are crucial for the ongoing progress and reliability of power electronic systems in various high-power applications.